Can Your Employees Actually Detect These Equipment Issues?
Cracked hoses, worn-out inflations, air bleeds—these are just a few of the common problems that can pop up when maintaining milking equipment. If left unchecked, they can lead to costly downtime, compromised milk quality and even animal health issues.
But the real question is: are your milkers trained to detect these issues early before they escalate? Ernest Hovingh, extension veterinarian at Pennsylvania State University, provides the following tips when it comes to training employees to spot and solve milking equipment problems when the arise.
The Big Four
“Milkers should also be trained to assess the basic condition and function of the milking equipment,” Hovingh says. “Some of the most common things that they should be looking for include blocked air bleed vents, cracked pulsation (short air) tubes, twisted inflations, and pinched hoses. While this may seem like an extensive list of things to check, once a milker is trained to be observant for these things, it can become second nature and does not require a lot of dedicated time or effort.”
He suggests training milkers to identify the following issues:
- Blocked Air Vents – Air vents in the claw or in the inflation are intended to create a deliberate ‘leak’ of air into the claw, to promote milk flow away from the claw and teat and into the milk hose, according to Hovingh. Occasionally, these vents can become blocked with debris, disrupting the flow of milk and increasing the risk of environmental mastitis. Hovingh recommends training milkers to identify where these vents are located and how to check to make sure they are functioning. “A small hiss of air can usually be heard being admitted into a functional vent, but if they are not sure if a vent is functioning properly, a small piece of a [milking] glove can be held up to the vent. If the vent is open, the glove should ‘stick’ to the vent.
- Cracked Tubes – Another common equipment problem Hovingh often sees are cracked short air tubes. These defective tubes can interfere with the pulsation of the liner and can prevent the vacuum from working correctly. “Milkers should be checking to see that the short air tubes are in good condition when they wash the milking clusters at the end of milking, but they should also be listening for vacuum leaks and looking for cracked tubes while milking,” Hovingh says. “Proactively changing the short air tubes on a regular schedule should also be part of the parlor maintenance routine.”
- Worn-out Inflations – During scheduled maintenance days, milking equipment companies will often provide a service of placing new liners into an additional set of shells so that the milkers simply only replace the shell and inflation as one unit. However, it’s important to ensure that inflations don’t become worn-out or misaligned. “Milkers should be checking to see that the alignment indicators on the inflations are lined up properly at least at the beginning of each milking,” Hovingh says. “Even with shell and inflations that have alignment notches, there can be some very obvious twisting problems with these units.”
- Pinched Hoses – Hoses that are too long or too short can often become pinched off during milking or wash cycles. This can result in reduced milk flow or un-sanitized equipment. “Milkers should be trained to watch for any restrictions/deformations in any hoses and immediately report them to the parlor manager,” Hovingh adds. “Regular inspections of all hoses every 2-4 weeks, and a regular replacement schedule are useful to prevent problems and allow for early identification.”
Dairy Herd Management, August 2024
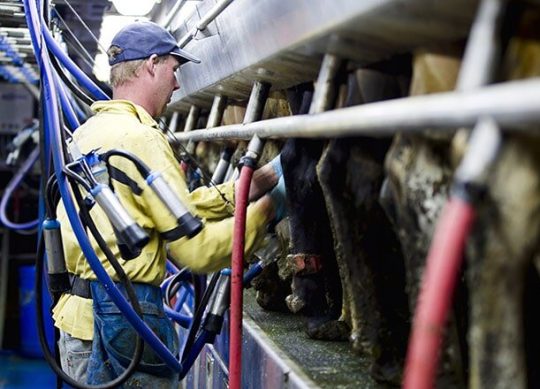